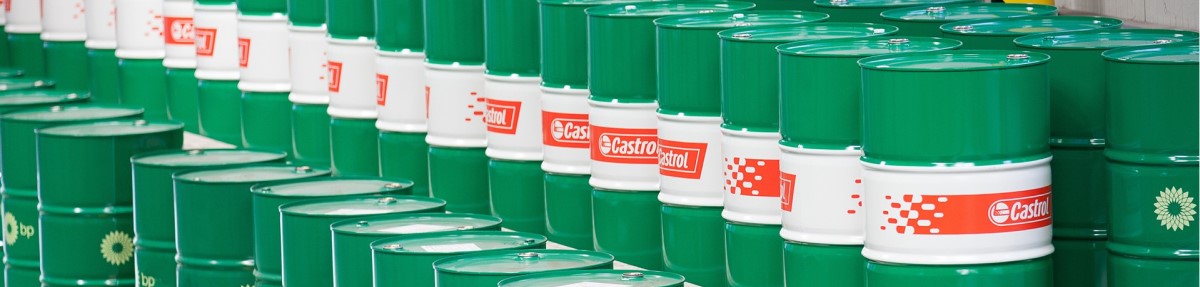
Als we praten over smeerolie, dan hebben we het al gauw over termen als mineraal, synthetisch en plantaardig, maar wat zijn nu eigenlijk de verschillen tussen de basisoliën en wat betekent dit voor u?
Soorten olie
Minerale basisolie is afkomstig van ruwe olie en kan een aantal smeereigenschappen hebben, afhankelijk van het raffinageniveau. Synthetische oliën worden door de mens gemaakt via een syntheseproces en hebben gewoonlijk betere eigenschappen dan minerale oliën. Plantaardige oliën hebben hun oorsprong in planten, die via chemische processen verwerkt worden. Deze worden meestal aangetroffen in bio-smeermiddelen.
Basisolie
Naast de basiscategorieën van basisoliën heeft het American Petroleum Institute (API) basisoliën in vijf groepen ingedeeld. De groepen I, II en III zijn allen op minerale basis.
- Groep I basisoliën worden geraffineerd met oplosmiddelen. Dit eenvoudige proces, dat al heel lang bestaat, verwijdert ongewenste bestanddelen zoals aromaten uit de olie. Groep I basisoliën zijn gewoonlijk voor minder dan 90% verzadigd, hebben een viscositeitsindex van 80 tot 120 en werken tussen 0 en 65 graden Celcius.
- Groep II basisoliën zijn minerale oliën die worden gemaakt met behulp van waterstofgas in een proces dat hydrogenatie of hydrokraken wordt genoemd. Dit is doeltreffender dan raffinage met oplosmiddelen om aromaten om te zetten in gewenste koolwaterstoffen.
- Groep III basisoliën worden verkregen via hetzelfde hydrogenatieproces, maar met extra warmte en druk. Hierdoor worden nog meer ongewenste bestanddelen omgezet en ontstaat een veel zuiverder basisolie met gewoonlijk meer dan 90% verzadigde bestanddelen en een viscositeitsindex van meer dan 120. Groep III oliën worden soms aangeprezen als synthetisch vanwege de toegenomen koolwaterstofmodificatie.
- Groep IV basisoliën zijn synthetische polyalfaolefinen (PAO). Dit zijn de meest gebruikte synthetische basisoliën, die worden gesynthetiseerd met behulp van ethyleengas. Deze basisoliën hebben een groter bedrijfstemperatuurbereik, een hogere viscositeitsindex en een grotere oxidatiestabiliteit dan minerale basisoliën. Groep IV-producten worden gewoonlijk gebruikt wanneer hoge temperaturen een rol spelen.
- Groep V omvat alle andere basisoliën, met name synthetische, waaronder polyalkyleenglycolen (PAG), siliconen en diësters.
Smeermiddelen
Hoewel de meesten van ons niet echt rekening houden met de basisolie die wordt gebruikt bij de samenstelling van onze smeermiddelen, is het vermeldenswaard dat een gemiddeld smeermiddel voor 90% uit basisolie en voor 10% uit additieven bestaat. Omdat de technologie voortdurend verandert en zich verder ontwikkelt, moeten smeermiddelen zich aanpassen en verbeteren om aan de eisen van machinefabrikanten te voldoen.
De meeste smeermiddelen die tegenwoordig in Europa verkrijgbaar zijn worden gemaakt met minimaal Groep II basisolie. Als u een smeermiddel zoekt dat onder extreme temperaturen of belastingen presteert, is een smeermiddel op basis van groep I of II wellicht niet geschikt. U zult ook merken dat smeermiddelen met verschillende basisoliën niet compatibel met elkaar zijn, wat bij vermenging tot een aantal problemen kan leiden. Dit geldt met name voor het hoofdbestanddeel van de olie – mineraal, synthetisch of plantaardig.
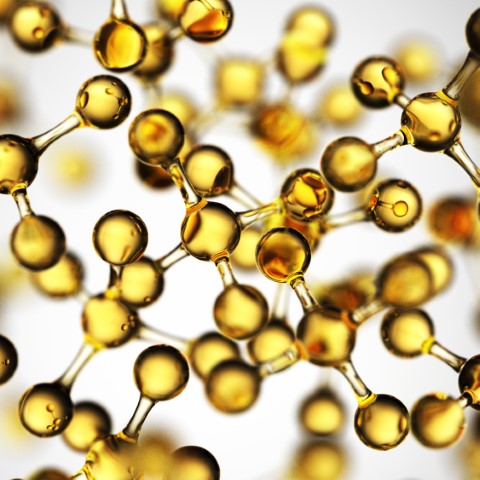
Het juiste smeermiddel
Inzicht in de voor- en nadelen van verschillende basisoliën kan ertoe bijdragen dat u de juiste smeermiddelen voor uw toepassingen kiest. Als u ooit twijfelt over het beste smeermiddel voor uw apparatuur of over de vraag of smeermiddelen mogen worden gemengd, raadpleeg dan de handleiding van uw apparatuur of overleg met uw smeermiddelen-partner.
Voor meer informatie kunt u altijd contact opnemen.
Volg KSM op LinkedIn
Meteen op de hoogte zijn van o.a. nieuwe producten en/of oplossingen, KSM nieuws en interessante artikelen/video’s? Volg ons dan via LinkedIn en ontvang automatisch updates.
Wilt u ook maximaal produceren tegen minimale kosten?
KSM heeft haar jarenlange ervaring en kennis, topkwaliteit producten én veelzijdige service gebundeld in de RCL (Reliability Centered Lubrication) methode. Hierdoor wordt stapsgewijs, zowel op product- als procesniveau, de klant begeleid naar het maximaal produceren tegen minimale kosten door middel van optimaal (smeertechnisch) onderhoud.
Het resultaat: productiemaximalisatie, een verlaging van risico’s en tot wel 30% kostenbesparingen.