Een zeer bekend gegeven binnen Lean Manufacturing is het zogenaamde principe van ‘Group Technology’. Hierbij worden verschillende werkstukken gegroepeerd om op een vaste set aan machines te produceren. Dit wordt ook wel vaak een ‘Productiecel’ genoemd. De reden om dit op deze wijze te doen is vanwege het feit dat aan gelijksoortige producten gelijke ontwerpeisen worden gesteld.
De inventarisatie
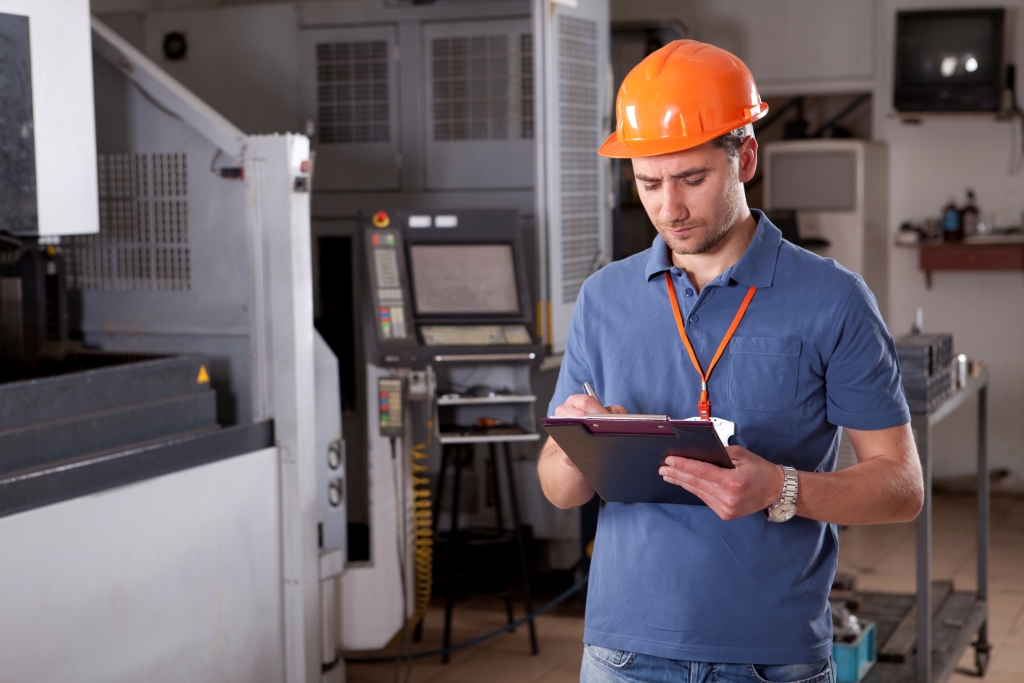
Deze analyse geeft o.a. antwoord op de volgende zaken:
– Om hoeveel verschillende werkstukken gaat het?
– Hoeveel productietijd (inclusief noodzakelijke doorlooptijd) is benodigd voor de productie?
– Welke nauwkeurigheids- en reinheidseisen worden er aan deze werkstukken gesteld?
– Hoeveel, en welke, opdrachtgevers betreft dit?
Het doel
Het doel van deze exercitie is om te kunnen bepalen of het rendabel is om een groep machines cq een ‘Productiecel’ vrij te maken voor clean verspaning en aanverwante werkprocessen. Is er voldoende werk om machines dedicated clean-grade te laten produceren, of is er voldoende potentie bij bestaande opdrachtgevers om ernaartoe te groeien, dan wordt het al snel aantrekkelijk om dit type productie te bundelen. De clean productie wordt dan gescheiden van de niet op clean gerichte productie. Deze laatste kan dan op andere machines cq een andere fysieke locatie worden geproduceerd. Voor de ‘Clean Productiecel’ kan in deze situatie een toegespitst werkproces worden ontwikkeld waarbij operatoren specifiek worden getraind in alle aspecten van het clean produceren.
Besparen op reinigingskosten
Net zoals bij de keuze van de beste verspaningsvloeistof voor clean produceren geldt ook hier: vooraf goed nadenken en het proces afstemmen op de te realiseren eisen kan heel veel moeite, kosten en doorlooptijd besparen.
Oftewel: een specifiek op clean produceren ingericht proces kan betekenen dat een werkstuk reeds meteen na productie aan de gestelde specs voldoet. Hiermee kunnen kostbare extra reinigingsprocessen, zoals die momenteel noodzakelijk zijn om een werkstuk ná productie alsnog aan de reinheidsspecs te laten voldoen, tot het verleden gaan behoren.
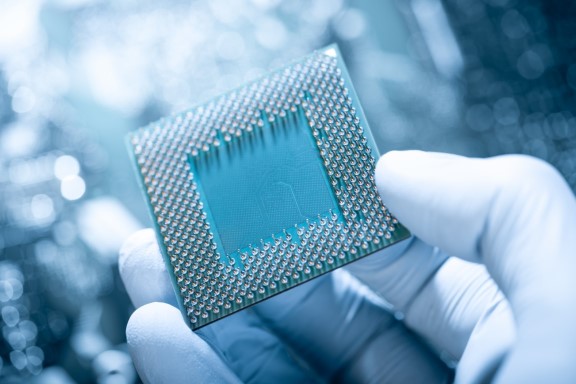
Voor meer informatie kunt u altijd contact opnemen.
Volg KSM op LinkedIn
Meteen op de hoogte zijn van o.a. nieuwe producten en/of oplossingen, KSM nieuws en interessante artikelen/video’s? Volg ons dan via LinkedIn en ontvang automatisch updates.
Wilt u ook maximaal produceren tegen minimale kosten?
KSM heeft haar jarenlange ervaring en kennis, topkwaliteit producten én veelzijdige service gebundeld in de RCL (Reliability Centered Lubrication) methode. Hierdoor wordt stapsgewijs, zowel op product- als procesniveau, de klant begeleid naar het maximaal produceren tegen minimale kosten door middel van optimaal (smeertechnisch) onderhoud.
Het resultaat: productiemaximalisatie, een verlaging van risico’s en tot wel 30% kostenbesparingen.