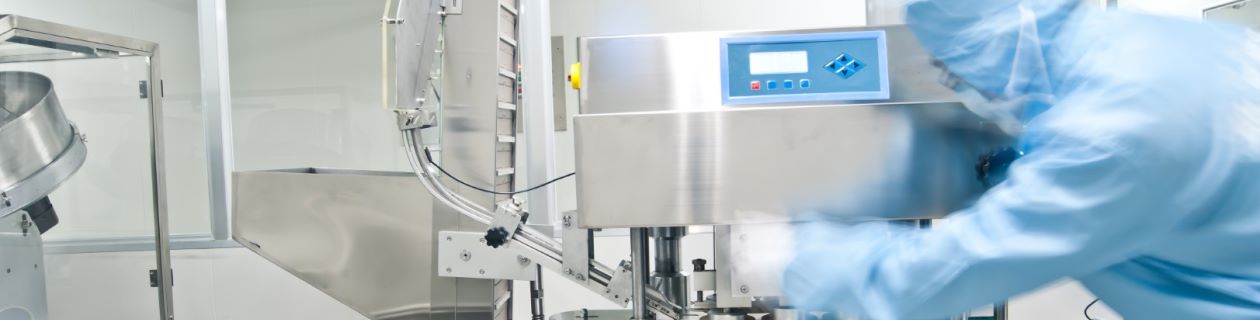
Iedereen heeft wel eens gehoord dat Lean Manufacturing één van de meest gerenommeerde methodes is om productieprocessen te optimaliseren. Ook is het algemeen redelijk bekend dat Lean Manufacturing werd ontwikkeld door Toyota. Niet voor niets wordt er dan ook vaak gesproken over processen ‘the Toyota way’ organiseren.
Wat minder mensen zich realiseren is wat deze methode met zich meebrengt. De automobiel-productie is bij uitstek een voorbeeld van een procesgedreven productie, waarbij de efficiency van de productie-assemblagelijn allesbepalend is. Je zou kunnen stellen een schoolvoorbeeld van een low-mix-high-volume (LMHV) productieproces. Als er echter iets is wat je juist niet kunt stellen bij verspaners, zeker niet wanneer zij te maken krijgen met cleanliness-uitdagingen, is procesgedreven massaproductie bedrijven. Specifieke uitzonderingen daargelaten draait het bij verspaners normaliter om high-mix-low-volume (HMLV) productie, met vaak vele honderden verschillende werkstukken voor talloze opdrachtgevers die jaarlijks worden geproduceerd.
Verspaners
Een aantal kenmerken die spelen bij verspaners zijn zoal:
- de vraagvariabiliteit is hoog;
- productieschema’s worden gestuurd door overeengekomen opleverdata;
- knelpunten in de productie kunnen in de loop van de tijd verschuiven;
- bestelhoeveelheden kunnen variëren van klein tot groot;
- levertijden die aan klanten worden opgegeven, moeten worden aangepast op basis van kennis van het productieschema.
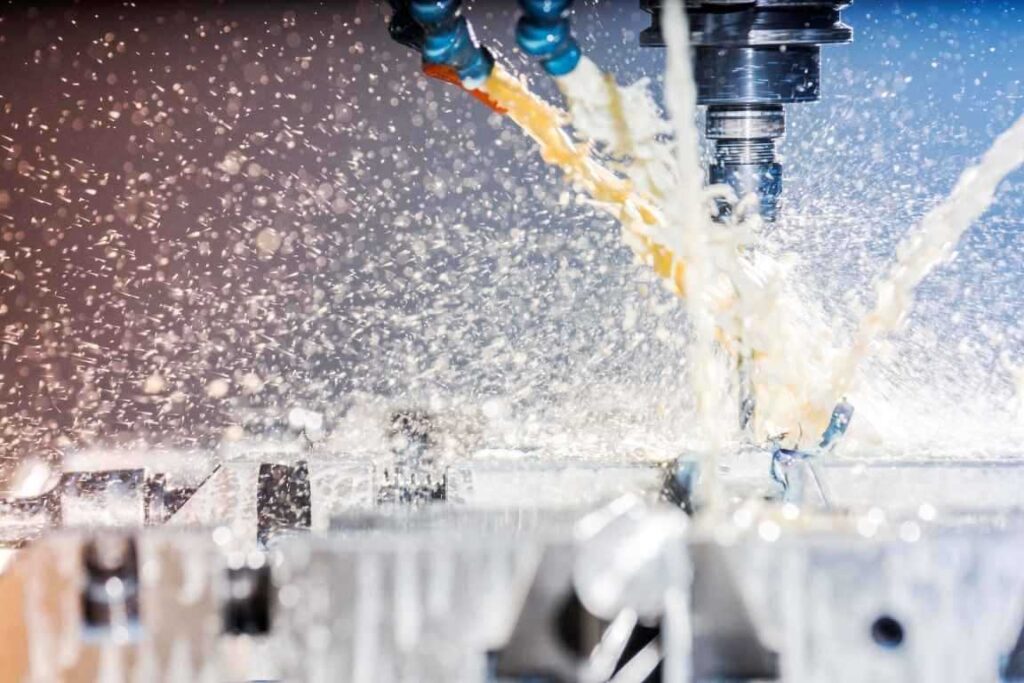
Daarnaast spelen ook onderstaande kenmerken een rol:
- het is moeilijk om het leveringsschema en de kwaliteit van de aanlevering vanuit leveranciers te beheersen;
- productiecontrole en -planning zijn complexer;
- de faciliteit heeft een functionele lay-out, waarbij de faciliteit is georganiseerd in afdelingen waar elke afdeling apparatuur heeft met identieke/gelijksoortige procesmogelijkheden.
Clean produceren
Vanwege de enorme variatie in werkstukken en navenant benodigde materialen, machines en bewerkingsstappen vormt de productieplanning een enorme opgave. Er zijn heel veel interne bewegingen en men heeft met te maken met enorme verspillingen, gelet op de 7 typen van verspilling die LEAN onderkent. Cleanliness eisen maken high-mix-low-volume (HMLV) productie nog ingewikkelder. Enerzijds door het introduceren van additionele processtappen gericht op controles en reinigingsstappen, anderzijds door hogere eisen die gesteld worden aan de procesinrichting en training van medewerkers om extra verspillingen te voorkomen.
Clean produceren ligt in dit kader met name grote druk om:
- Defecten te voorkomen. Het kan hierbij gaan om producten die off-spec zijn vanuit technisch oogpunt en/of reinheidsoogpunt;
- Onnodige transportbewegingen te voorkomen. Dit betreft intern transport van het ene productiestation naar de volgende, maar ook zaken als externe transportbewegingen naar bijvoorbeeld een cleaning-partner;
- Het voorkomen van onnodig complexe processen, waarbij contaminatie van werkstukken verwijderd dient te worden die eerder in het proces veroorzaakt is en welke voorkomen had kunnen worden.
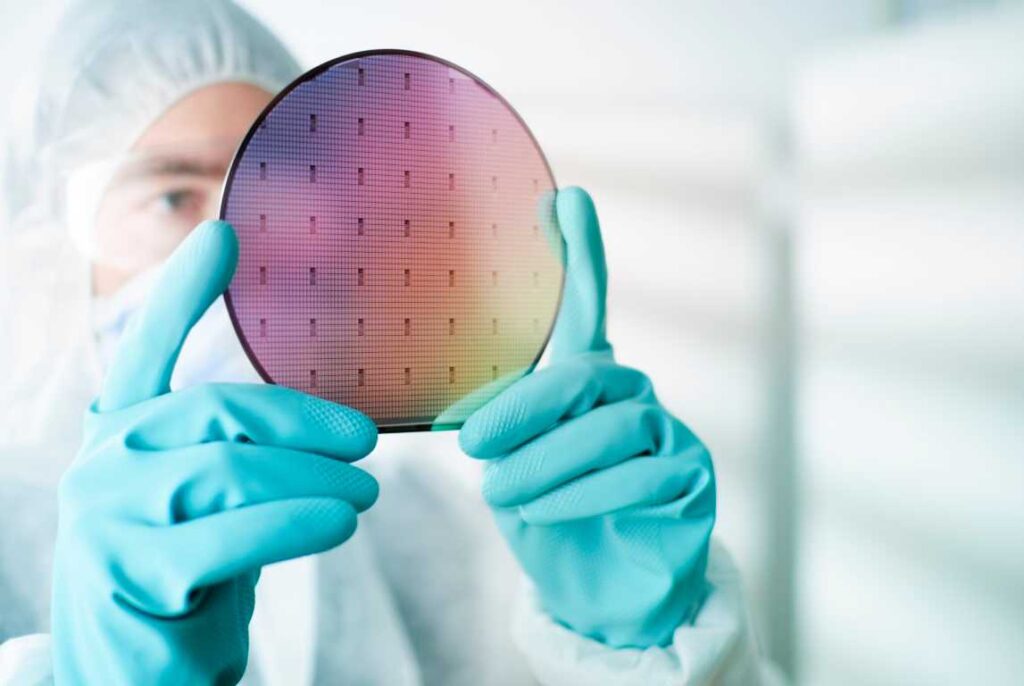
Kosten en tijdverlies niet als 'gegeven' beschouwen
Processen dienen altijd geoptimaliseerd te worden met de klanteisen voor ogen, waarbij de bestaande werkwijze ter discussie mag staan en verspillingen voorkomen dienen te worden. Kosten en tijdverlies zijn in niemands’ belang, waarom zou je ze dan als een gegeven beschouwen?
Voor meer informatie kunt u altijd contact opnemen.
Volg KSM op LinkedIn
Meteen op de hoogte zijn van o.a. nieuwe producten en/of oplossingen, KSM nieuws en interessante artikelen/video’s? Volg ons dan via LinkedIn en ontvang automatisch updates.
Wilt u ook maximaal produceren tegen minimale kosten?
KSM heeft haar jarenlange ervaring en kennis, topkwaliteit producten én veelzijdige service gebundeld in de RCL (Reliability Centered Lubrication) methode. Hierdoor wordt stapsgewijs, zowel op product- als procesniveau, de klant begeleid naar het maximaal produceren tegen minimale kosten door middel van optimaal (smeertechnisch) onderhoud.
Het resultaat: productiemaximalisatie, een verlaging van risico’s en tot wel 30% kostenbesparingen.