Quaker Houghton Hocut 5019 voorkomt oplossen kobalt in vloeistof
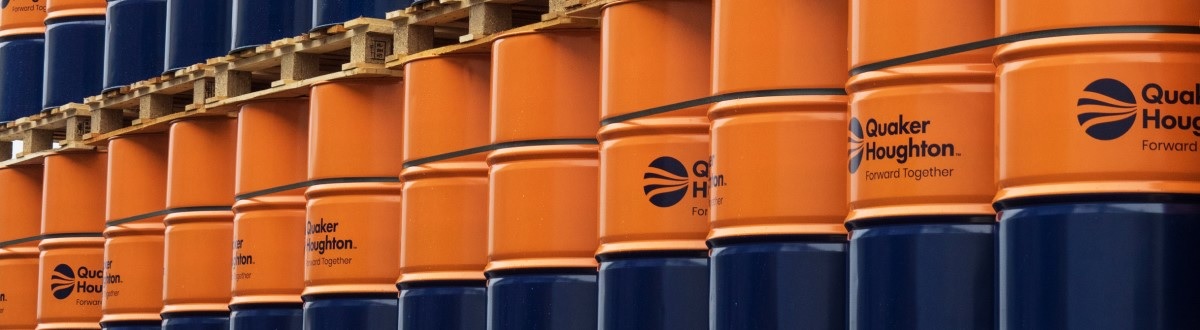
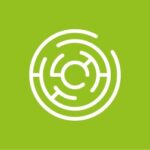
De uitdaging
Een internationaal toonaangevend familiebedrijf dat kwalitatief hoogwaardige machinemessen, zagen, rakels en precisie-slijtdelen voor technische doeleinden produceert en verkoopt had te kampen met twee uitdagingen. Enerzijds bereikte de concurrerende slijpvloeistof (20 m3 in een centraal systeem) nooit de gewenste levensduur, ondanks de inzet van zeer geavanceerde filtratietechnieken. Anderzijds speelde er vanwege het oplossen van kobalt, afkomstig uit het hardmetaal dat werd geslepen, een uitdaging op het gebied van HSSE.
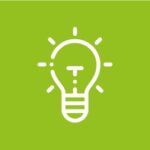
De oplossing
Mede op basis van de ervaringen zoals die bij onze partner Quaker Houghton reeds waren opgedaan heeft KSM een aantal adviezen verstrekt over de wijze waarop beide uitdagingen aangepakt kunnen worden. Een onderdeel van die adviezen was het inzetten van Quaker Houghton Hocut 5019, een vol-synthetische vloeistof die o.a. wordt aanbevolen voor het slijpen van wolfraamcarbide werkstukken waarin kobalt verwerkt is. Het speciale additievenpakket voorkomt daarbij het oplossen van kobalt in de vloeistof.
Na uitgebreid testen op een stand-alone machine én continue opvolging van de resultaten is uiteindelijk besloten om het centraal systeem te reinigen en over te schakelen naar de Hocut 5019.
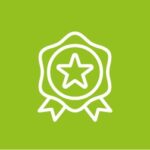
Het resultaat
- Zeer goede resultaten in de slijpprocessen, minder slijtage gereedschappen;
- Geen kobalt meer in de vloeistof aanwezig, goed voor gezondheid en welzijn van operators;
- De levensduur van de vloeistof is meer dan verdubbeld, jaarlijkse kostenbesparing (buiten stilstand gedurende reiniging en verversing) ca. € 17.000,-.
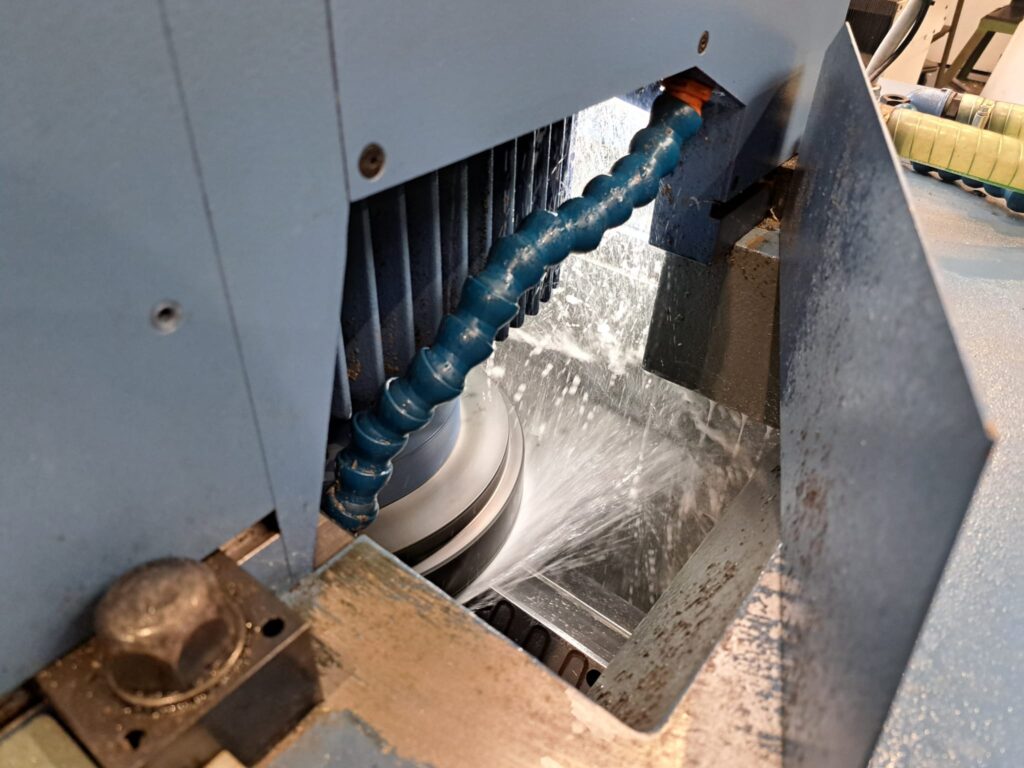
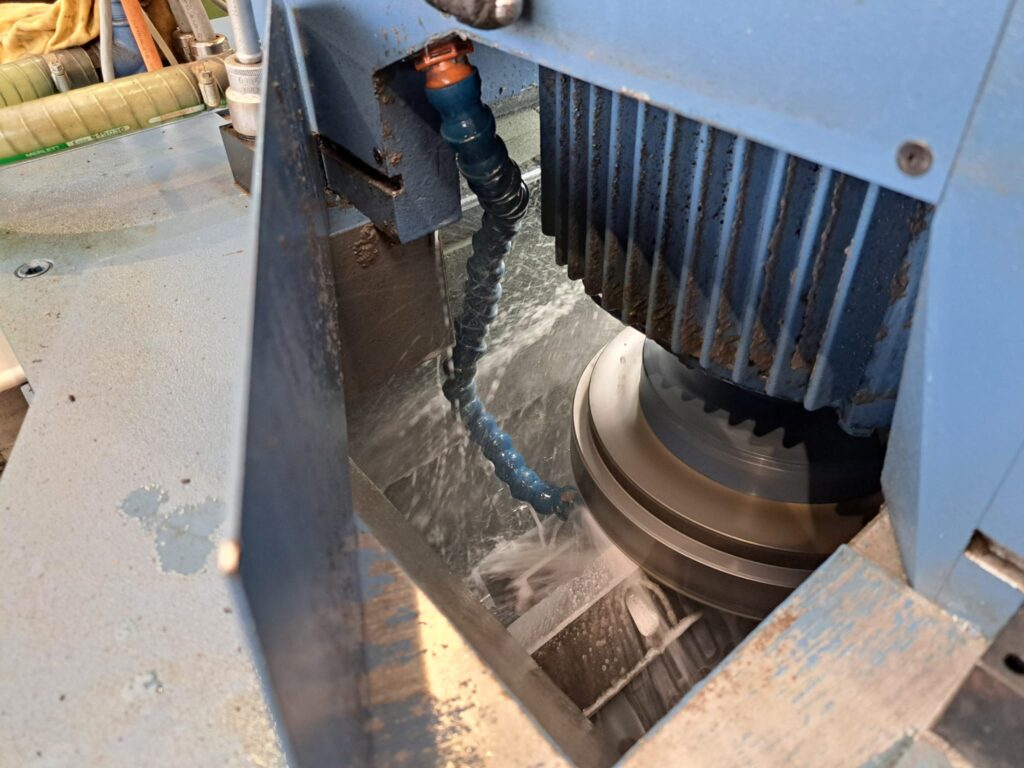
Voor meer informatie kunt u altijd contact opnemen.
Volg KSM op LinkedIn
Meteen op de hoogte zijn van o.a. nieuwe producten en/of oplossingen, KSM nieuws en interessante artikelen/video’s? Volg ons dan via LinkedIn en ontvang automatisch updates.
Wilt u ook maximaal produceren tegen minimale kosten?
KSM heeft haar jarenlange ervaring en kennis, topkwaliteit producten én veelzijdige service gebundeld in de RCL (Reliability Centered Lubrication) methode. Hierdoor wordt stapsgewijs, zowel op product- als procesniveau, de klant begeleid naar het maximaal produceren tegen minimale kosten door middel van optimaal (smeertechnisch) onderhoud.
Het resultaat: productiemaximalisatie, een verlaging van risico’s en tot wel 30% kostenbesparingen.