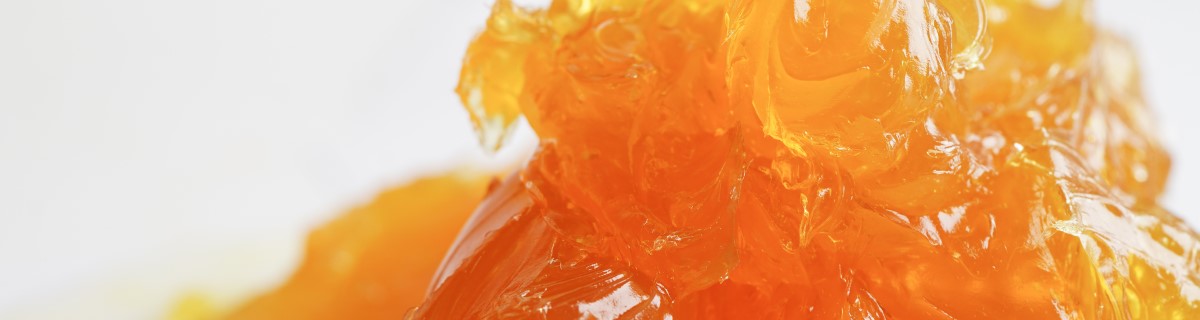
Onderhoudsdiensten gebruiken vaak smeervetten die ‘altijd al worden gebruikt’. Dat hoeft geen probleem te zijn, maar het kan voorkomen dat er inmiddels betere producten beschikbaar zijn, of dat er een ander smeermiddel nodig is omdat de applicatie onder andere omstandigheden wordt gebruikt. Drie belangrijke punten bij de keuze voor een smeervet zijn de component zelf, de temperatuur en de omgeving.
Uitgangspunten bij vetsmering
Om te beginnen bij de component: vooraf moet de logische vraag worden gesteld “wat gaat er precies gesmeerd worden”? Bijna 90% van de smeervetten is geschikt voor toepassing in verschillende soorten lagers, overbrengingen en koppelingen. Vervolgens is het belangrijk om de grootte van de component te bekijken en de snelheid waarmee hij beweegt. Beide factoren zijn gerelateerd aan de sterkte en de dikte van de smeerfilm. Met relatief eenvoudige formules is vervolgens de gewenste viscositeit vast te stellen. Verder speelt de belasting een rol in de keuze van het juiste smeermiddel: in extreme gevallen kunnen additieven uitkomst bieden bij sterke slijtage en extreme druk. Trillingen vergen aparte aandacht omdat zij kunnen leiden tot grote problemen, zoals lekkage en een verhoogde vetafscheiding. Een voldoende hoge viscositeit en een goede mechanische stabiliteit leveren vaak goede resultaten. Bij automatische smeersystemen is het verder van belang dat de eigenschappen van geschikte vetten juist tegengesteld zijn aan die voor het smeren van lagers. Het is dus belangrijk om na te gaan of deze combinatie mogelijk is in de betreffende applicatie.
Temperatuur en omgeving
De universeel toepasbare smeervetten zijn geschikt voor temperaturen tussen grofweg -30 en 120 °C. Problemen ontstaan vooral bij de aangegeven grenzen. Er zijn weinig applicaties waarbij smeren onder de -30 °C is vereist. Wanneer dit toch aan de orde is, zijn hoge opstartkoppels en problemen met centrale smeersystemen veelgehoorde problemen. Het is dus belangrijk om in deze gevallen te kiezen voor een smeermiddel voor lage temperaturen. Wanneer het om hogere temperaturen gaat, is vooral een reductie van de levensduur van het smeermiddel één van de belangrijkste problemen. Echte problemen treden op bij temperaturen van 150 – 200 °C of hoger. Ook hier is het belangrijk een speciaal smeermiddel te kiezen, en vooral zeer frequent te controleren of er nog voldoende smeermiddel met de gewenste eigenschappen beschikbaar is. De invloed van de omgeving is tot slot één van de meest gecompliceerde parameters, die helaas te vaak wordt genegeerd. De belangrijkste omgeving-gerelateerde problemen hangen samen met de aanwezigheid van water. Water kan immers het vet wegspoelen, de smeerfilm beschadigen of corrosie veroorzaken. Dat is vooral het geval bij toepassingen in sectoren als de scheepvaart en papierindustrie, niet in de laatste plaats omdat smeermiddelen daar ook veelvuldig blootstaan aan andere vormen van vervuiling.
Ontbrekende kennis
Heeft de eindgebruiker voldoende kennis van smeermiddelen om de juiste keuze te maken voor zijn specifieke applicatie? De praktijk wijst uit dat bij eindgebruikers regelmatig onvoldoende productkennis aanwezig is met betrekking tot het kiezen van het juiste smeermiddel. Vaak wordt met een bepaald smeermiddel gesmeerd ‘omdat dit al jaren zo gebeurt’. Ook blijkt regelmatig dat op de werkplek weinig kennis aanwezig is ten aanzien van de verschillende producten (en hun specifieke kenmerken) die verkrijgbaar zijn. Hierdoor ontstaat terughoudendheid in het gebruik van andere, modernere en betere producten. De gevolgen van onjuist smeermiddelgebruik zijn weliswaar meestal niet direct zichtbaar, maar kunnen groot zijn. Wat dat betreft doen eindgebruikers er goed aan zich uitgebreid te laten adviseren over het juiste smeermiddel of de combinatie van smeermiddelen (ofwel de compatibiliteit), met name bij het overschakelen naar een ander product. Overigens is het voor een eindgebruiker sowieso erg nuttig het smeermiddelenprogramma van tijd tot tijd te evalueren. Dit alleen al vanuit het oogpunt van kostenbesparing, waarbij de nadruk dan vooral dient te liggen op de totale kosten. Een relatief kostbaar smeermiddel kan zich immers in bepaalde applicaties prima terugbetalen door het reduceren van de onderhoudskosten en het verhogen van de beschikbaarheid en betrouwbaarheid van de machine.
Keuze smeervet
Welk smeervet geschikt is voor een bepaalde applicatie, wordt in eerste instantie bepaald door de constructeur. De aanbevolen producten worden vervolgens veelal vastgelegd in de vorm van OEM specificaties. Wanneer die informatie echter ontbreekt is de combinatie verdikkertype, basisolieviscositeit en gebruikte additieven voor een groot deel bepalend of het product geschikt is of niet. Daarnaast is het van belang dat bekend is op welke wijze het smeervet moet worden toegepast. De hoeveelheid gebruikt product is namelijk van essentieel belang voor een optimale smering, want zowel te veel als te weinig smeervet is ongunstig. Ook dient de gebruiksomgeving zo schoon mogelijk te zijn om daarmee de kans op contaminatie te minimaliseren. Ten slotte is het van het uiterste belang dat de op de werkplek circulerende onderhoudsaanbevelingen en onderhoudslijsten up-to-date zijn en de juiste producten bevatten. Klinkt op zich heel logisch en vanzelfsprekend, maar helaas wil de praktijk nog wel eens anders uitwijzen.
Bron: TIM – Marjolein de Wit – Blok
Voor meer informatie kunt u altijd contact opnemen.
Volg KSM op LinkedIn
Meteen op de hoogte zijn van o.a. nieuwe producten en/of oplossingen, KSM nieuws en interessante artikelen/video’s? Volg ons dan via LinkedIn en ontvang automatisch updates.
Wilt u ook maximaal produceren tegen minimale kosten?
KSM heeft haar jarenlange ervaring en kennis, topkwaliteit producten én veelzijdige service gebundeld in de RCL (Reliability Centered Lubrication) methode. Hierdoor wordt stapsgewijs, zowel op product- als procesniveau, de klant begeleid naar het maximaal produceren tegen minimale kosten door middel van optimaal (smeertechnisch) onderhoud.
Het resultaat: productiemaximalisatie, een verlaging van risico’s en tot wel 30% kostenbesparingen.