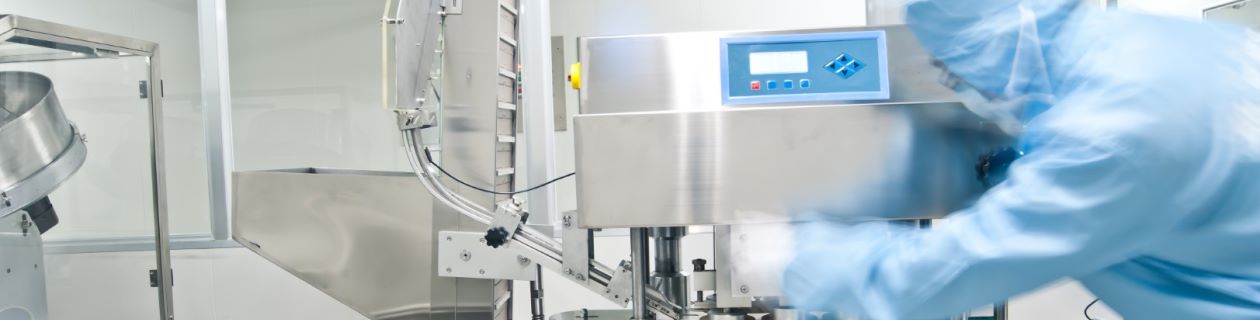
In een serie artikelen worden een groot aantal tips toegelicht waar verspaners hun voordeel mee kunnen doen bij clean produceren. In ‘tip 3’ een overzicht van welke Lean tools wél en niet/minder geschikt zijn voor verspaners.
Stappenplan
Bij de implementatie van ‘LEAN Manufacturing’ wordt standaard een 5-stappen proces doorlopen. Dit proces is bedacht door de LEAN-pioniers James Womack en Daniel Jones. Onderstaand volgt een overzicht van de betreffende vijf stappen:
- Identificeer waar waarde te vinden is
Specificeer waarde vanuit het standpunt van de opdrachtgever. Doe dit voor iedere productfamilie die vervaardigd wordt. - Breng de waardestroom in kaart
Identificeer voor elke productfamilie alle stappen in de waardestroom en elimineer waar mogelijk de stappen die geen waarde creëren. - Creëer ‘Flow’
Zorg ervoor dat de stappen voor het creëren van waarde in een strakke volgorde plaatsvinden, zodat de werkstukken in een vloeiend proces richting de eindfase bewegen.
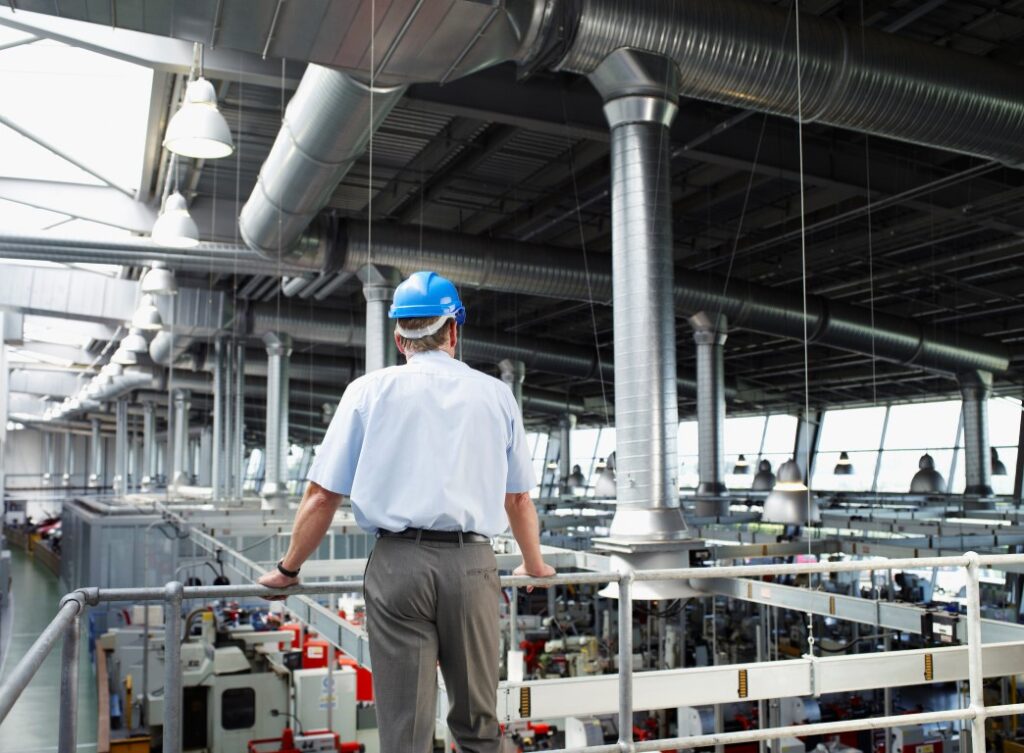
- Breng ‘Pull’ tot stand
Produceer producten alleen wanneer de opdrachtgever daar behoefte aan heeft. De opdrachtgever trekt de producten als het ware uit het proces naar zich toe. - Optimaliseer en zoek perfectie
Naarmate de waarde wordt gespecificeerd, worden waardestromen geïdentificeerd, verspillingen verwijderd en flow gecreëerd. Als het proces is afgerond, begin dan van voren af aan en doorloop de stappen telkens weer opnieuw, totdat de meest ideaal haalbare situatie is bereikt waarbij maximale waarde wordt gecreëerd met minimale verspilling.
Lean Manufacturing: tools
LEAN Manufacturing omvat tientallen tools die je in staat stellen om analyses en verbeteringen door te voeren. Omwille van de high-mix-low-volume dynamiek die doorgaans bij verspaners speelt, zie daarvoor ook Lean & Clean tip 2, zijn een aantal van deze tools heel goed inzetbaar en sommige juist niet. Onderstaande tools zijn bijvoobeeld heel goed toepasbaar binnen de werkprocessen en omgeving bij verspaners:
- 5S
De 5S-methode verwijst naar vijf Japanse en Engelse termen die beginnen met een ‘S’ en een methode voor de organisatie van de werkplek bieden. Deze zijn respectievelijk:
- Scheiden (Seiri);
- Sorteren (Seiton);
- Schoonmaken (Seiso);
- Standaardiseren (Seiketsu);
- Standhouden (Shitsuke).
- Total Productive Maintenance (TPM)
TPM is een tool om het stilstaan van machines in het productieproces te voorkomen. Het omvat drie hoofdelementen:
- preventief onderhoud;
- corrigerend onderhoud;
- onderhoudspreventie.
Vanuit onderhoudsperspectief gezien wordt TPM overtroffen door RCM3 (Reliability Centered Maintenance 3e generatie) waar ook KSM’s smeermethodiek op gebaseerd is.
- SMED
SMED staat voor Single-Minute Exchange of Dies. Het doel van SMED is om alle overschakelingen en startups terug te brengen. Door de installatietijd te verkorten, kunnen fabrieken de efficiëntie aanzienlijk verbeteren. De belangrijkste principes zijn hierbij:- overschakelingen identificeren;
- analyseren van elke taak om het doel te bepalen;
- goedkope oplossingen bepalen;
- verkorten van de omsteltijd.
- Poka-Yoke
Het doel is om een vorm van kwaliteitscontrole te creëren die defecten zichtbaar maakt en voorkomt dat deze de klant bereiken. Het richt zich vooral op menselijke fouten die kunnen ontstaan in het proces en die niet helemaal te voorkomen zijn.
- Visueel Management
Visual Management is een communicatietechniek die visuele hulpmiddelen gebruikt om berichten sneller en efficiënter over te brengen. Doelstellingen zijn hierbij:- verduidelijken waar verspillingen liggen;
- problemen weergeven op een eenvoudiger manier;
- duidelijk aangeven wat de doelen van continue verbeteren zijn;
- vergroten van de effectiviteit van communicatie.
- 8 Verspillingen theorie
Lean manufacturing verwijst 8 verspillingen (voorheen waren het er 7) naar acht typische plaatsen waar verspillingen in processen optreden. Wat zijn de acht verspillingen: 1 overproductie, 2 wachten, 3 transport, 4 overbewerking, 5 onnodige voorraad, 6 beweging, 7 defecten en 8 talent.
- Jidoka
Bij Jidoka worden processen gemonitord en wordt bij een afwijking of probleem het productieproces gestopt om het op te lossen. Aansluitend start een onderzoek om toekomstige problemen te voorkomen. Door zo snel mogelijk (in het proces) in te grijpen worden toekomstige afwijkingen voorkomen. Het doel is defectvrij te produceren.
- Gestandaardiseerd werk
Gestandaardiseerd werk binnen Lean Manufacturing is een laagdrempelig hulpmiddel om de huidige beste werkwijzen te documenteren, de standaard te verbeteren en ervoor te zorgen dat de nieuwe standaard een basis voor verbetering wordt. Gestandaardiseerd werk verbetert drie belangrijke aspecten van het productieproces:- de snelheid waarmee producten worden geproduceerd om aan de vraag van de klant te voldoen;
- de werkvolgorde van de operator om producten tegen die tijdswaarde te produceren;
- de standaard inventaris die nodig is om een soepel productieproces te garanderen.
- Cellular Manufacturing
Cellular Manufacturing is het proces waarbij vergelijkbare producten in één cel worden geproduceerd. Het product doorloopt het productieproces daardoor zonder onderbrekingen. In Cellular Manufacturing kunnen vergelijkbare producten op dezelfde assemblagelijn worden geproduceerd.
- 6 Six Big Losses theorie
Six Big Losses verwijst naar de zes meest voorkomende redenen voor niet-effectieve productie. Wat zijn de Six Big Losses:- 1: wachten;
- 2: ombouwen;
- 3: vertraagde snelheid;
- 4: korte stops;
- 5: afkeur/herbewerken
- 6: in-/uitloopverlies.
Lean modellen in relatie tot clean verspanen
Vele van deze tools en modellen verdienen een nadere uitleg. Deze volgen uiteraard later in deze serie artikelen. Samenvattend kun je echter stellen dat veel LEAN modellen, maar zeker niet alle, toe te passen zijn binnen high-mix-low-volume bedrijven. Alhoewel de situatie in de fabriek veel complexer is dan bijvoorbeeld binnen de procesindustrie, gaat ook hier de aandacht uit naar het optimaliseren van processen en werkwijzes door de mensen op de vloer.
Het uiteindelijke doel: alle stappen geoptimaliseerd en kosten en risico’s waar mogelijk te elimineren. Bij CLEAN verspaners kijken we achtereenvolgens naar de pre-productiefase, productiefase, de cleaningfase, assemblage en verzendfase en (parallel aan al deze fases) de ketensamenwerking. Zijn deze fases bij u al optimaal ingericht?
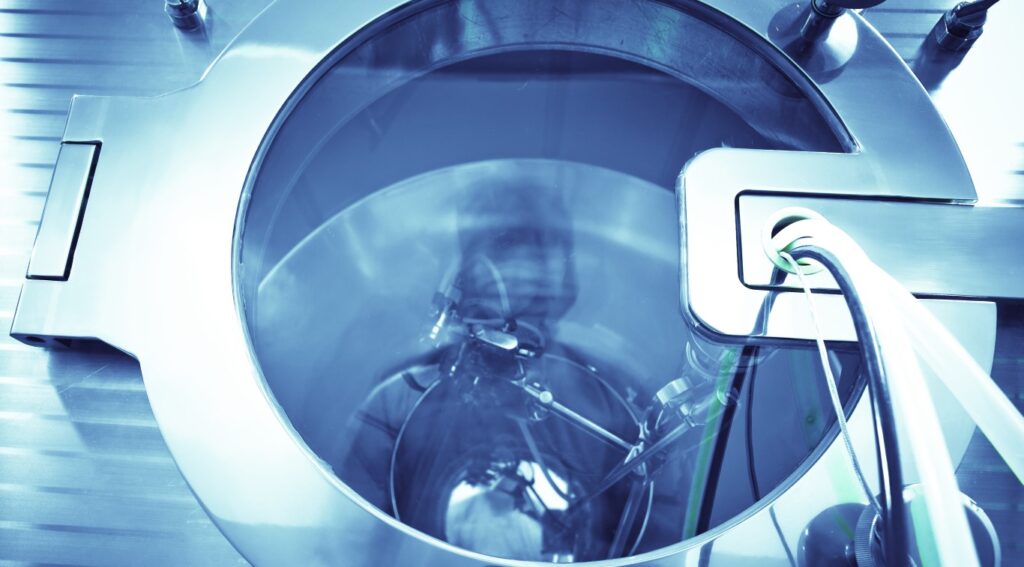
Voor meer informatie kunt u altijd contact opnemen.
Volg KSM op LinkedIn
Meteen op de hoogte zijn van o.a. nieuwe producten en/of oplossingen, KSM nieuws en interessante artikelen/video’s? Volg ons dan via LinkedIn en ontvang automatisch updates.
Wilt u ook maximaal produceren tegen minimale kosten?
KSM heeft haar jarenlange ervaring en kennis, topkwaliteit producten én veelzijdige service gebundeld in de RCL (Reliability Centered Lubrication) methode. Hierdoor wordt stapsgewijs, zowel op product- als procesniveau, de klant begeleid naar het maximaal produceren tegen minimale kosten door middel van optimaal (smeertechnisch) onderhoud.
Het resultaat: productiemaximalisatie, een verlaging van risico’s en tot wel 30% kostenbesparingen.